Table Of Contents:
- RFID Textile Tracking for Hotels and Apparel Rental Businesses: Automating Linen, Uniform, and Garment Management
- The Problem: Inefficiencies and Losses in Textile Management
- What Drives These Challenges?
- Why RFID Is the Right Tool for the Job
- Results: What RFID Delivers to Hotels and Apparel Rental Businesses
- Why Now: The Pressure to Modernize
- Recommendation: How Invento RFID Can Help
- Final Thoughts
- Frequently Asked Questions
How RFID Automates Textile Tracking for Hotels and Apparel Rental Businesses
The textile management industry for hotels and apparel rental businesses faces challenges that impact operational efficiency and profitability. Inefficient management of linens, uniforms, and other garments leads to losses through misplacement, overstocking, and underutilization, affecting customer satisfaction and increasing costs. In an industry where turnaround time and service quality are critical, traditional manual systems cannot meet the demand for speed, accuracy, and accountability. This article explores how can transform textile management by automating processes, reducing losses, and streamlining inventory control. It covers the core problems, key challenges, the benefits of RFID technology, and how Invento RFID solutions can modernize operations while providing sustainability and traceability throughout the item lifecycle.
The Problem: Inefficiencies and Losses in Textile Management
Textile management in hospitality and rental sectors suffers from operational issues that lead to financial losses and service disruptions. Inefficient tracking results in misplaced items, inventory discrepancies, and unaccounted losses. Manual processes using paper logs or outdated barcodes delay order fulfillment and cause errors during returns. For instance, hotels and rental businesses often overstock some items while running out of others due to inaccurate inventory counts, directly affecting service quality and costing more in operations.
The lack of traceability further complicates identifying issues in the supply chain, leading to recurring losses and reduced items lifespan due to frequent laundering and wear. Errors such as misplaced tags or manual data entry create additional discrepancies, hampering decision making related to inventory management and procurement. Without an integrated automated system, crucial data—usage patterns, maintenance schedules, and lifecycle management—remains incomplete, forcing businesses to react rather than proactively manage resources.
What Drives These Challenges?
Several factors drive challenges in textile management. Traditional inventory methods based on manual counts and paper systems are prone to human error, producing discrepancies between actual and recorded inventories. This inaccuracy is a leading cause of shortages and overstocking.
The dynamic usage environment adds complexity. Hotels constantly circulate linens and uniforms, while rental demand fluctuates with seasons and events. Without real-time tracking, managing inventory levels is nearly impossible. Variability in washing schedules, damage rates, and replacements further complicates matters; for example, a lost uniform during a busy season can result in immediate shortages affecting service quality.
Legacy systems that lack integration with modern platforms produce siloed and inaccurate data, making predictive maintenance and supply forecasting challenging. Coupled with the need to meet high standards of cleanliness and availability, these inefficiencies can negatively affect customer experience. Advances in technology such as IoT and AI increase expectations for real-time supply chain visibility, yet without modern integration, businesses cannot fully leverage these benefits.
RFID: The Technology Behind Smarter Tracking
RFID, or Radio Frequency Identification, is an innovative technology that has revolutionized the way businesses and industries track and manage assets. Utilizing electromagnetic fields, RFID enables automatic identification and data capture through embedded tags. These tags consist of small radio transponders that communicate with readers to relay information about the tagged object. By eliminating the need for manual scanning processes, RFID streamlines operations, enhances inventory management, and significantly reduces the risk of human error. This technology is widely adopted in various sectors, including retail, healthcare, logistics, and manufacturing, where precision and efficiency are paramount.
RFID Laundry Tags for Reliable Textile Identification & Tracking
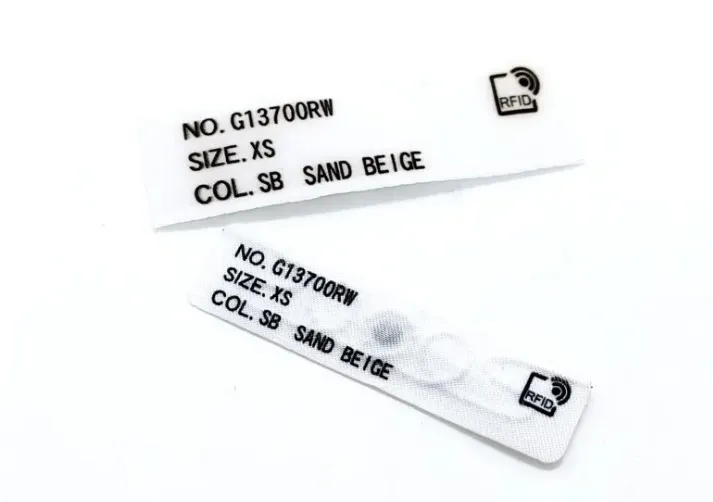
RFID laundry tags are specially engineered to withstand the harsh conditions of industrial washing, drying, and ironing, including repeated exposure to water, heat, pressure, and chemicals. Built for durability, these tags can endure more than 200 wash cycles, making them ideal for identifying and tracking textiles in high-turnover environments such as commercial laundries, hotels, and apparel rental operations. These durable, sew-in or heat-sealable tags contain a small RFID chip and antenna that allow for non-contact, bulk reading — even when embedded in wet, folded, or bagged garments. Operating typically in the UHF (Ultra High Frequency) range, RFID laundry tags offer fast read rates and high reliability, enabling real-time inventory visibility, automated sorting, and accurate traceability throughout the textile lifecycle.
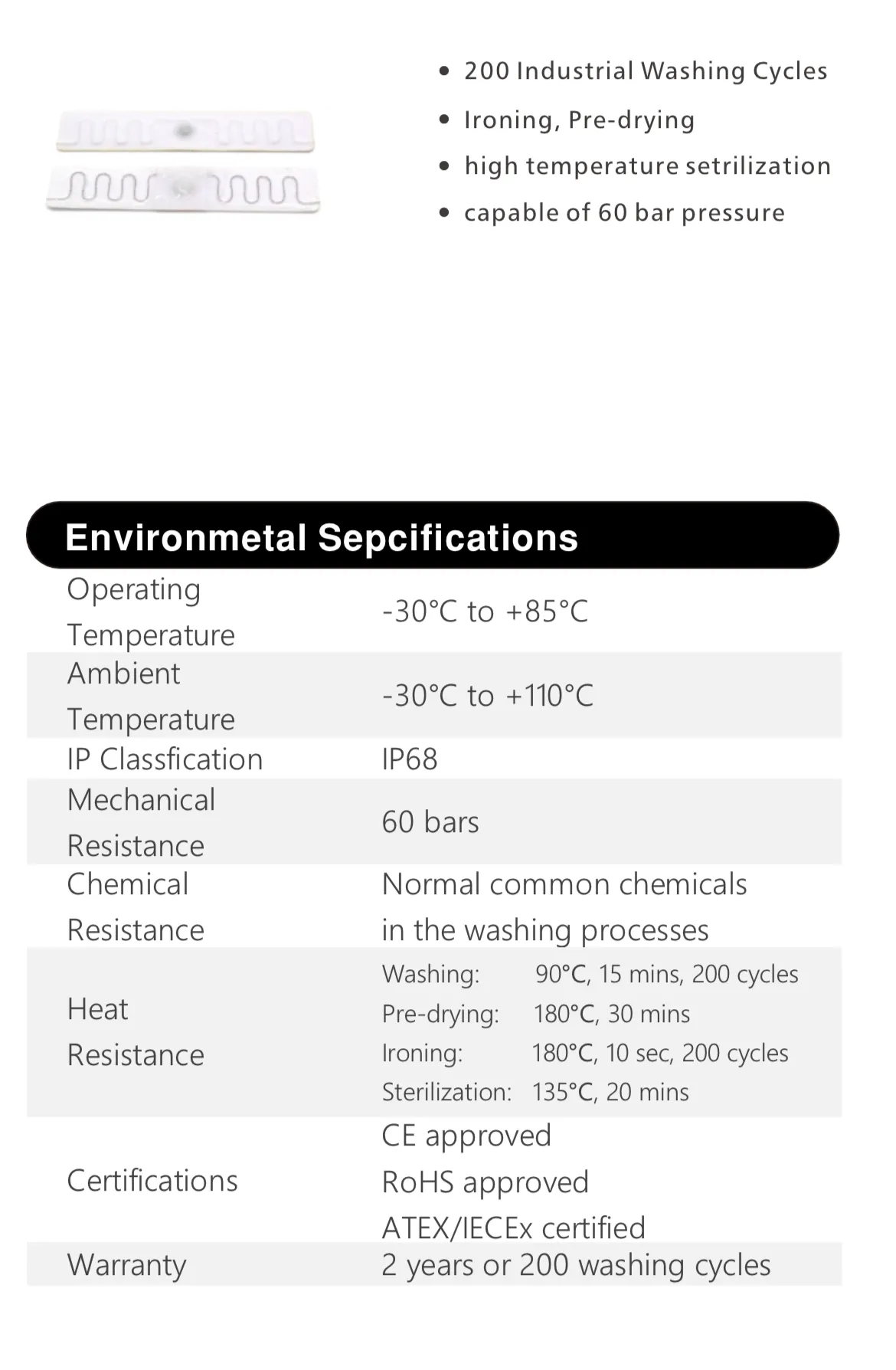
What Can You Track Using RFID Laundry Resistant Tags?
RFID laundry-resistant tags can be used to track a wide range of textile items commonly found in hotels, hospitals, industrial laundries, and apparel rental businesses. You can track linens, towels, bedsheets, pillowcases, tablecloths, uniforms, workwear, scrubs, spa robes, costumes, and rental garments — all without manual scanning. Each item embedded with a tag can be read remotely and in bulk using fixed or handheld RFID readers, allowing for streamlined inventory audits, automated sortation, loss prevention, and lifecycle tracking. This not only improves operational efficiency but also supports better forecasting, billing accuracy, and accountability in high-turnover textile environments.
Why RFID Is the Right Tool for the Job
RFID offers a transformative solution for textile management. By using passive RFID tags and readers, fixed or portable antennas, and the right tracking and inventory management software, RFID systems ensure real-time, automated tracking of items throughout their lifecycle. This minimizes human error, reduces manual labor, and guarantees that each linen, uniform, or garment is accurately accounted for.
Real-Time Visibility and Automation at Every Stage
RFID automates inventory audits, tracks items during laundering, and updates counts in real time. This immediate data enables efficient stock management and informed decision-making. For example, when a hotel laundry processes thousands of linens, an RFID system quickly registers each item’s entry and exit, reducing processing times and errors.
Data-Driven Insights for Smarter Operations and Sustainability
RFID supports predictive maintenance by collecting usage and wash cycle data. This insight helps identify patterns that cause premature wear, guiding timely repairs or replacements. The technology integrates smoothly with modern cloud-based management systems, offering analytics for order fulfillment and enhanced supply chain management and transparency. Such a holistic view of assets improves overall operational efficiency and reduces costs.
RFID also enhances traceability, crucial for meeting environmental and regulatory standards. Greater transparency supports sustainability initiatives by tracking materials from procurement to recycling, helping with the appropriate sorting of materials and supporting a circular economy. In short, RFID automates critical processes, boosts real-time visibility, minimizes losses, and supports both operational and sustainability goals.
What RFID Delivers to Hotels and Apparel Rental Businesses
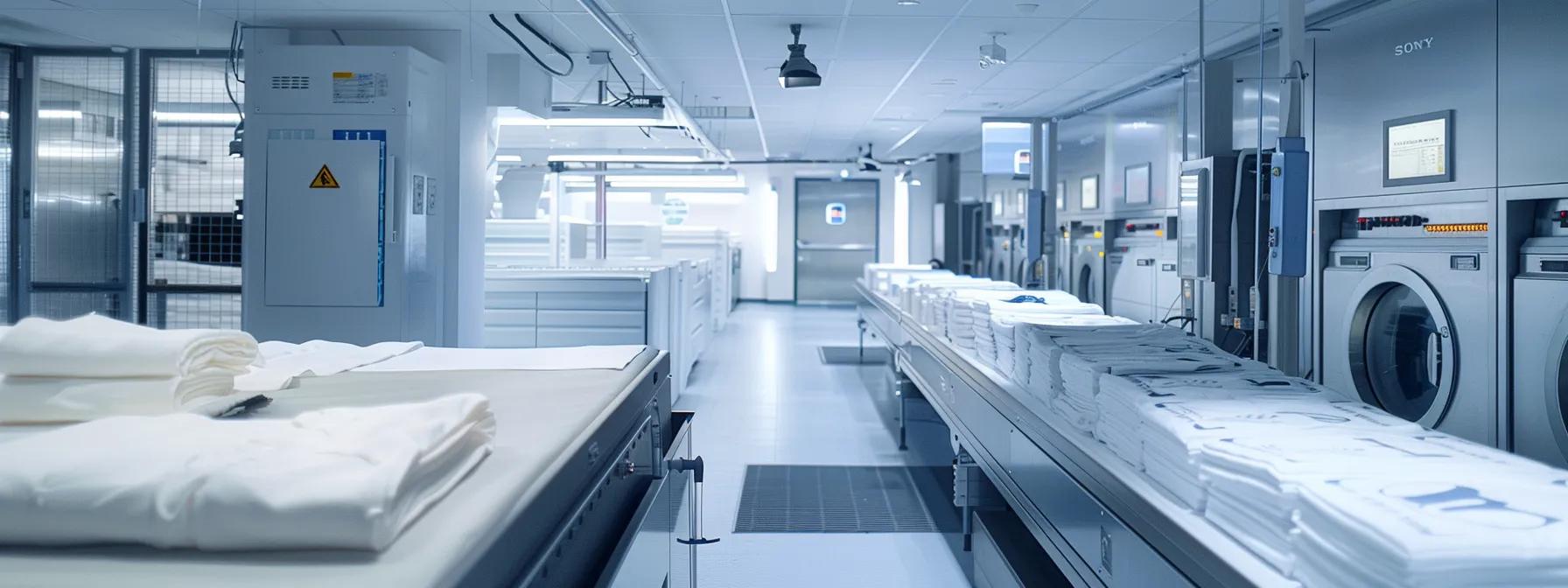
Implementing RFID technology transforms textile operations in several ways. One of the main benefits is a significant reduction in inventory discrepancies. Real-time tracking ensures that every textile—whether in use, in the wash, or stored—is accurately counted, reducing overstock and minimizing losses from misplaced or damaged items.
RFID boosts operational efficiency by enabling faster turnaround times. Automated tracking helps items move seamlessly through every stage of the operation and supply chain, cutting the need for manual checks and speeding up processes like the laundry cycle. When RFID readers scan a batch of linens, the central database is updated instantly, ensuring that property managers always know which items are available.
The technology also improves asset utilization and lifespan. With continuous monitoring, hotels and rental businesses can perform proactive maintenance and schedule timely replacements, leading to long-term cost savings and more sustainable practices. Furthermore, RFID data assists in forecasting demand and optimizing purchasing decisions, reducing unnecessary expenditures and waste.
Beyond inventory management, RFID enhances security and loss prevention. With a detailed audit trail for each item, it becomes easier to spot and address anomalies such as theft or misplacement. This added accountability supports regulatory compliance and quality control, while also improving customer satisfaction by reducing service delays and enforcing high-quality standards.
List of Key Results Delivered by RFID:
- Enhanced Inventory Accuracy – Automated counts reduce human error.
- Reduced Operational Costs – Streamlined processes lower labor expenses and mismanagement losses.
- Improved Turnaround Times – Faster processing accelerates laundry cycles and restocking.
- Extended Asset Lifespan – Continuous monitoring enables timely maintenance and replacements.
- Increased Security – Real-time tracking and audit trails help prevent theft and misplacement.
Comparative Benefits of RFID vs. Traditional Textile Management Systems
Parameter | Traditional System | RFID-Enabled System | Improvement (%) |
---|---|---|---|
Inventory Accuracy | 70-80% | 98-99% | +25-30% |
Processing Time | 15-20 minutes per batch | 5-7 minutes per batch | -60% time reduction |
Asset Utilization | Low tracking efficiency | Real-time tracking | +40% efficiency gain |
Loss Prevention | High misplacement rates | Comprehensive audit trail | +50% reduction |
Labor Dependency | High manual intervention | Automated data capture | -70% manual effort |
The table demonstrates significant improvements offered by RFID over traditional textile management methods, leading to cost savings, improved service levels, and higher customer satisfaction.
Why Now: The Pressure to Modernize
Modernizing textile management has become imperative. With increased pressure to improve efficiency, reduce waste, and enhance customer service, outdated manual systems are a liability. The digital revolution and IoT advancements demand operational transparency, pushing businesses to adopt advanced technologies to stay competitive.
Rising operational costs associated with manual tracking create a strong financial argument for automation. When profit margins are slim, methods that cut costs while boosting accuracy become essential. Real-time data is also crucial for optimizing supply chain processes. RFID’s live data feeds about asset locations and usage meet this need, helping businesses react swiftly to changing market demands.
Meeting Compliance Today While Preparing for Tomorrow
Regulatory pressures and sustainability commitments further drive the need for modern systems. Customers now demand ethical practices and transparency, and RFID supports digital traceability (such as) that tracks items from procurement to recycling. In addition, emerging technologies like artificial intelligence and blockchain, which enhance predictive maintenance and resource allocation, are best leveraged through an integrated RFID system. Thus, now is the optimal time to transition to an automated RFID system that not only meets current demands but also positions a business for future growth.
Recommendation: How Invento RFID Can Help
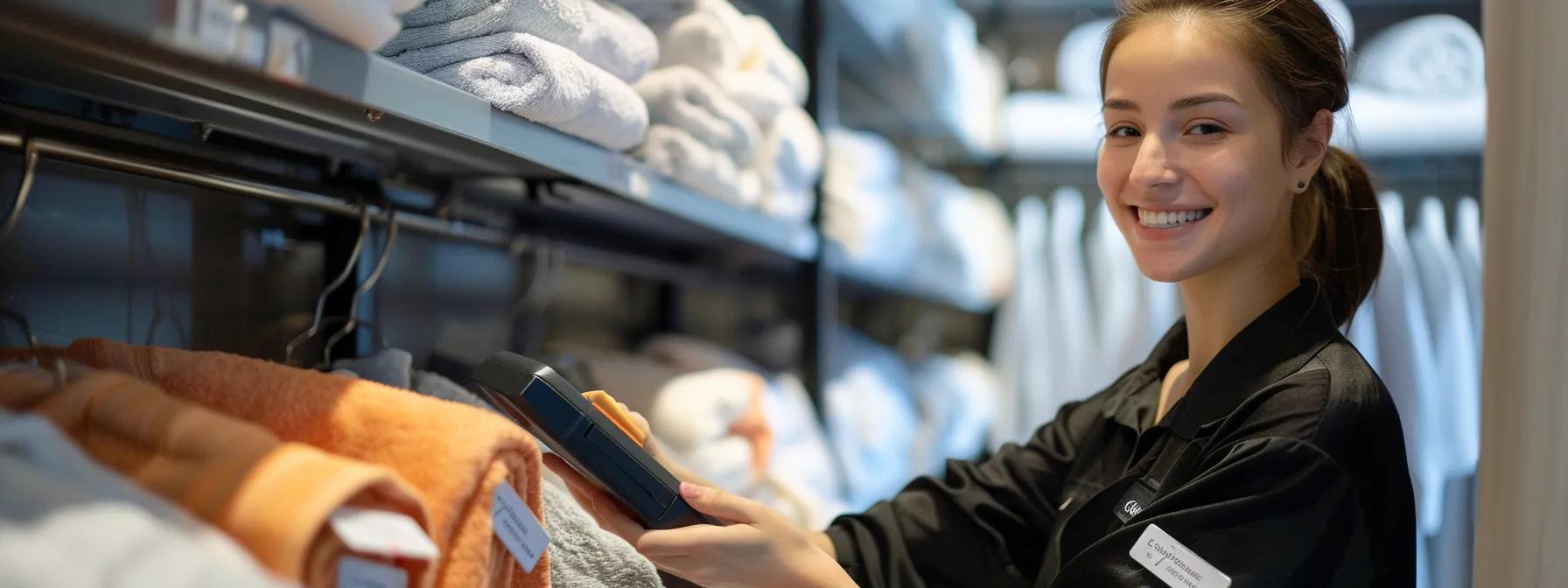
Invento RFID delivers a cutting-edge solution tailored to the unique textile management challenges faced by hospitality and apparel rental businesses. With a proven record in for the apparel industry, Invento’s system integrates easily into existing workflows, delivering instant and actionable insights into textile assets.
The system automates data capture, offering real-time updates on every item’s status—whether in use, laundered, or stored—which drastically reduces human error and eliminates tedious manual counts. Using ultra high frequency (UHF) passive RFID tags that withstand frequent laundering, the system pairs robust readers with inventory management software that consolidates data into an intuitive dashboard for seamless tracking and management.
Moreover, Invento RFID deepens supply chain integration by linking RFID data with warehouse management systems and ERP software, enhancing traceability and enabling predictive maintenance. Its analytical tools help forecast demand, optimize inventory levels, and reduce waste, leading to substantial cost savings over time.
The solution also promotes sustainability by ensuring textiles are fully tracked and efficiently recycled at the end of their lifecycle. Their Digital Product Passport feature provides complete visibility into an item’s journey, verifying compliance with environmental regulations while supporting a circular economy. Enhanced by blockchain security, every transaction is transparent and tamper-proof.
Engineered for versatility, Invento RFID suits both small-scale and large enterprise operations. Its scalable architecture grows with your business, managing increasing inventory volumes without loss of performance. Overall, Invento RFID transforms textile management into a streamlined, efficient operation that reduces costs and elevates service quality, making it a future-proof investment for any forward-thinking operational manager.
Final Thoughts
Textile management inefficiencies have long plagued hotels and apparel rental businesses, driving up costs and compromising service quality. RFID technology directly addresses these issues by automating tracking, enhancing accuracy, and providing real-time inventory insights. With its robust integration into existing management platforms, Invento RFID not only modernizes operations but also lays the groundwork for a sustainable future. Adopting this technology is a strategic investment in long-term efficiency and improved customer satisfaction.
Frequently Asked Questions
Q: How does RFID improve inventory accuracy in textile management? A: RFID uses passive tags that automatically track the location and movement of textiles in real time, reducing human error and ensuring consistently accurate inventory counts.
Q: What specific challenges in textile management does RFID address? A: RFID tackles manual tracking errors, inefficient inventory audits, slow turnaround times in laundry processes, and loss prevention by automating data capture and integrating with supply chain systems.
Q: Can RFID systems handle the harsh environments of laundry and frequent use? A: Yes, RFID systems for textile management use durable UHF passive tags designed to withstand frequent washing, high temperatures, and chemical exposure.
Q: How does Invento RFID integrate with existing management systems? A: Invento RFID seamlessly interfaces with warehouse management systems and ERP software, facilitating real-time data sharing and advanced analytics for quick, informed decision-making.
Q: What cost savings can be expected from implementing an RFID textile tracking system? A: Businesses typically experience significant reductions in labor costs, fewer losses from misplacements, and more efficient asset lifecycle management, all contributing to a strong return on investment.
Q: How does RFID support sustainability in textile management? A: By ensuring accurate tracking throughout a textile’s lifecycle and supporting efficient recycling and proper disposal, RFID helps companies meet environmental regulations and contribute to a circular economy through features like the Digital Product Passport.
Q: What types of businesses benefit most from RFID textile tracking? A: Hotels, apparel rental businesses, and any operations with high-volume textile usage benefit from RFID tracking as it improves operational efficiency, enhances customer service, and reduces overall costs